6271
EXPLOSION HAZARDS AND PROTECTION IN THE USE OF INTERMEDIATE BULK CONTAINERS (part II)
03/06/2018
Filling represents the most hazardous operation since the material under- goes dispersion and can therefore acquire charge during the separation processes occurring in transport. The bulk material and its associated charge are then packed into a small space. Here, the charge is not able to flow to the ground quickly enough, even with a conductive and grounded receiver. This generates a high space charge density and electric field. In addition to charge accumulation there can be problems due to heat accumulation and the possibility of entrainment of smouldering lumps. Charging processes in FIBC Any powdered insulating material filled into an FIBC is likely to acquire electric charge. Any insulating material will acquire an electrical charge when contacted and separated from another material; the process is called contact electrification. Relative movement of the two surfaces during contact generally enhances the charging effect; this is called triboelectrification. During FIBC filling, the product will typically pass through ducts and the particles will constantly collide with the surfaces of the ducts and with each other. There is plenty of opportunity for the filling product to become charged. As the charged product enters the FIBC, the surface of the container will become charged in a number of ways. Triboelectrification of the container surfaces will occur as the product collides with the surfaces, charge may migrate to the container surface from the charged filling product and corona charging may occur. The latter charging is as a result of the bulking together of the charged product in the container to form a cone. At the tip of the cone the field from the charge on the product is concentrated and may reach the breakdown value for air. Charge released in the air is repelled from the cone and may build up on the surface of the container. If powder is charged when it enters the FIBC then the insulating properties of the
standard polypropylene FIBC will cause charge to accumulate in the bag as more powder is added. Under conditions of exceptionally high charging, for example following pneumatic transfer of powder, the charge levels on the powder can be so high that the com- pacted powder produces electric field strengths both inside and outside the bag which can exceed the dielectric strength of air. The rate at which charge dissipates depends on the
electrical resistance between the stored charge and ground. An electrostatic spark occurs when an isolated charged object is suddenly grounded. For air, the breakdown strength is approximately 3000 kV /m.
Assessment of the electrostatic ignition risk in powder handling plants requires a decision as to whether a dust cloud can be ignited by brush or propagating brush discharge, spark, cone or corona.
Brush discharges can occur from the bulk product or from the highly insulating surface of the FIBC or the liner and have an energy content of up to 3 or 4 mJ. Propagating brush discharges may occur across the FIBC fabric or liner if the FIBC is filled with a highly charged product and the breakdown voltage of the FIBC wall includ- ing the coating and liner exceeds 4 kV. They have much higher energies than ordinary brush discharges and occur if a double layer of charges of opposite polarity is generated across a thin sheet of a non-conducting material for example, across an insulating FIBC wall. This type of discharge is capable of igniting dusts. Propagating brush discharges may only occur during the filling and emptying of FIBC with highly charged, highly insulating product. Propagating brush discharges may be excluded if the volume of resistivity of the fabric is lower than about 10 8
Ohm or if the breakdown voltage across the FIBC fabric is less than 4 kV. Spark discharges from a conductive FIBC or a conductive part that is not earthed are able to ignite dusts. An electrically insulating bag (standard polypropylene) which has become contaminated with a conducting substance, such as water, may also be capable of producing spark discharges from the contaminated area to any nearby earth. If the conductive bag is earthed then spark discharges from the bag are not possible. Spark discharges from a charged conductive product are possible but can be excluded by using earthed conductive FIBC or by introducing an earthed metal rod down to the
bottom of an insulating FIBC prior to filling. Spark discharges from a person or other external conductive object can be excluded by earthing the person or object.
Cone discharges can occur across the surface of the powder heap in the FIBC. Cone discharges can be a little more energetic than brush discharges, but their limiting energy is dependent on the diameter of the bag being filled as well as the particle size of the powder. Corona discharges are associated with conductors with sharp points or edges. They can occur when such an earthed electrode moves towards a highly charged object or when the conductor is raised to a high potential. The very weak gas discharge or corona from the sharp point of the conductor occurs with a constant discharge over a long time with an extremely low energy and is only capable of igniting extremely sensitive flammable gas air mixtures. A summary of the main types of discharge that may occur when filling or emptying FIBC is shown in Table 1. If the bag receiving the powder is made from a conducting material that is connected to earth, then brush and propagating brush discharges from the bag fabric are no longer possible. External bag contamination and external object charging by induction are also no longer relevant.
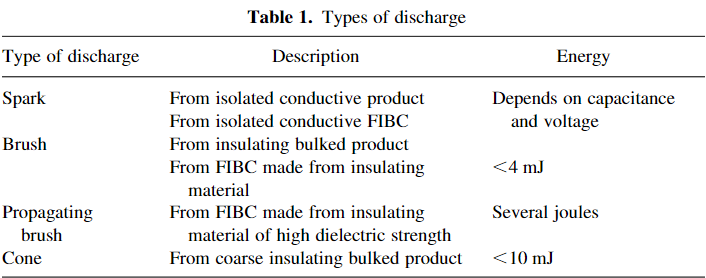
If the bag is not earthed or becomes disconnected from earth then ener-getic spark discharges can occur under certain conditions. During emptying, which couldtake as little as 15 seconds, electrostatic charging mechanisms will again be present.Classification of FIBCThree common terms used in the FIBC industry are 100% plastic FIBC, antistatic FIBCand fully conductive FIBC.
i, 100% plastic FIBCare collapsible, rectilinear plastic containers. The typical designcomprises a bi-directional polypropylene weave plus a facing of polypropylene orpolyethylene film of specified thickness on one or both sides. While they may benitrogen purged prior to filling, they cannot be grounded.
ii, Antistatic FIBCusually contains conductive threads or aluminized surfaces that areelectrically connected to one or more grounding connections. Conductive threadsmay run in the warp or the weft direction, or both. Antistatic FIBC have alsobeen produced with antistatic coatings or with ungrounded systems of isolatedconductive threads, which limit charge accumulation by corona discharge andhave an intrinsically low capacitance.
iii,Fully conductive FIBCcontain sufficiently high loadings of conductive material(typically carbon black) to render all the plastic conductive.
Classification of FIBC according to their ability to avoid electrostatic hazards have beenmade by divided them into four types: A, B, C and D.Type AFIBC have a woven structure with no electrical-property specification.This type is intended for use in situations where there are no risks from electrostaticdischarges. They are suitable only with non-flammable products in non-flammableenvironments.Type BFIBC are non-conductive, but have the added requirement that the fabricwall has a breakdown voltage of less than 4 kV to prevent the occurrence of a propagatingbrush discharge. Use of a standard non-conducting plastic liner may raise the wall break-down voltage to above 4 kV, raising the possibility that a propagating brush dischargecould occur at high filling rates or emptying.Type CFIBC are designed to be electrically conductive and have a resistance toearth from any location on the FIBC, including the slings, of less than 108Ohm. Typically,Type C contain a matrix of conductive fibres within the synthetic-fibre weave terminatingin a conductive strip that is earthed during filling or emptying. Some bags carry the con-ductive strip into the lifting loops so that the bag will be grounded when hung on agrounded loading/unloading station. Using a Type C bag requires permanent groundingof the bag during the whole period while the bag is filled or discharged. The dischargefrom an ungrounded bag aligns to a single discharge point and such a discharge may bestrong enough to ignite dust clouds.Type DFIBC have conductive threads that are not interconnected and may also havea partially conductive coating. They are electrostatically-dissipative bags and it is claimedthat no grounding is required since special static-dissipative fibres and antistatic coatings are present to safely dissipate electrostatic charges by a combination of corona dischargeand enhanced surface conductivity. There is no specification for the electrical propertiesfor the fabric of a static dissipative bag. Instead, each design is qualified by special testprocedures in which the propensity of “worst-case” bag discharges to ignite flammablegases with known ignition energies are investigated. Typically the system of conductivefibres has a capacitance too small to give incendive sparks at the maximum voltageattained; the latter is limited by corona discharge above 1 – 2 kV plus the action of a anti-static agent applied to the fabric. There is some controversy surrounding the Type D bag,the Hazardous Cargo Bulletin(1)reported concerns over reports that using the unearthedType D bag can cause ignitions in atmospheres with minimum ignition energies of lessthan 0.25 mJ.
NON-ELECTROSTATIC IGNITION SOURCES
Potential sources of ignition classified as non-electrostatic and likely to be relevant to IBCinclude open flames, hot surfaces, mechanical sparks, arcs from electrical equipment andself-heating of solids. The HSE gives practical advice and application of the law relating tothe control and prevention of these ignition sources(2).Many incidents have been caused by careless use of welding or flame cutting equip-ment, or other hot work. Sparks can travel long distances, particularly if work is carried outat a high level. It is therefore important that hot work is effectively isolated from bag fillingoperations.The requirements for protected electrical equipment for use in atmospheres offlammable dusts are given in BS 6467: Parts 1 and 2 (1985 and 1988). Advice is givenon the design, selection, installation and maintenance of equipment. The main factors tocontrol are the maximum surface temperature and restriction of dust ingress to theenclosure.It is preferable to site electrical equipment away from dusty areas, but if installationis close to dusty areas, a dust tight enclosure is recommended to prevent the risk of dustignition inside the apparatus. BS EN 60529 classifies types of enclosures and gives theman index of protection.It is necessary to ensure that the maximum surface temperature produced by an itemof electrical equipment exposed to dust is below that required to ignite the dust either as alayer or as a cloud.Many materials are prone to spontaneous heating, which may be caused by airoxidation, biological reaction or exothermic decomposition. Where materials may behandled hot, for example in a drying process prior to discharge into an IBC, maximumtemperatures need to be controlled.Ignitions have occurred as a result of burning or smouldering material from anupstream process. Potential risks from smouldering material can be reduced by isolationmethods, i.e. slam-shut valves or by methods of interlocking, i.e. power isolation fromrotary valves.
to be continued...
Source: P Holbrow Health and Safety Laboratory, Harpur Hill, Buxton, SK17 9JN SYMPOSIUM SERIES No. 150
Registered
4
Average
daily search
71%
Effective
search
213
Registered
companies
You are using BETA version.
Send feedback